Load Cell for Tubing Belt Scale - A New Continuous Weighing Method
The tubing belt has attracted wide attention for its environmental protection, moisture-proof and high efficiency. At present, there is a new technology that directly conveys the clinker lime powder to the steel plant in a sealed way by tubing belt, it successfully breaks the traditional dynamic measurement method of electronic belt scale, but uses two weighing hoppers to weigh in turn statically, thus achieving the goal of continuous, fast and accurate measurement.
I. Scheme and Composition
Basic design scheme: Material (lime powder) conveyed by the tubing belt is continuously conveyed to two weighing hoppers respectively, and the two weighing hoppers conducts static weighing in turn under a working mode of alternate loading and unloading, quick unloading and slow loading. The time interval from quick unloading and slow loading ensures the static weighing of weighing hopper while guaranteeing the continuous conveying of materials on the tubing belt, thus realizing the continuous, fast and accurate weighing measurement.
The system consists of two weighing hoppers, control devices, video and remote devices. The system structure of tubing belt scale is shown on figure 1.
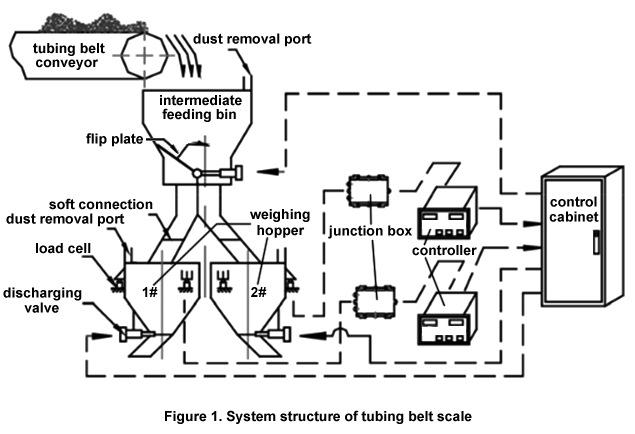
1. Weighing hopper
Weighing hopper is composed of load cell, weighing controller and limit device, configuration of the weighing hopper should meet the technical requirements of corresponding accuracy grade.
1.1 Selection of load cell
The load cell should be column type load cells or shear beam load cells with good side load and impact resistance, easy installation and maintenance.
The main technical parameters of column type load cells: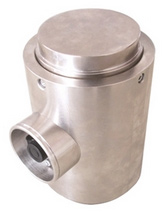
The main technical parameters:
The weighing system uses a collision-type limit device that is mounted near the load cell. The collision type limit can limit load cell movement on horizontal direction and provide support protection to the hopper on vertical direction due to the inclination of load cell. The load cell controller displays the accumulated weight on the large screen in the field through 0-20mA signal output. The system is well grounded to ensure that the system is effective in preventing lightning strikes.
2. Control device
The control device consists of intermediate feeding bin, material feeding and discharging valve and control equipment. A flip plate is set inside the intermediate feeding bin to control the material feeding of weighing hopper 1# and 2#, the material feeding and discharging valve may be electric or pneumatic.
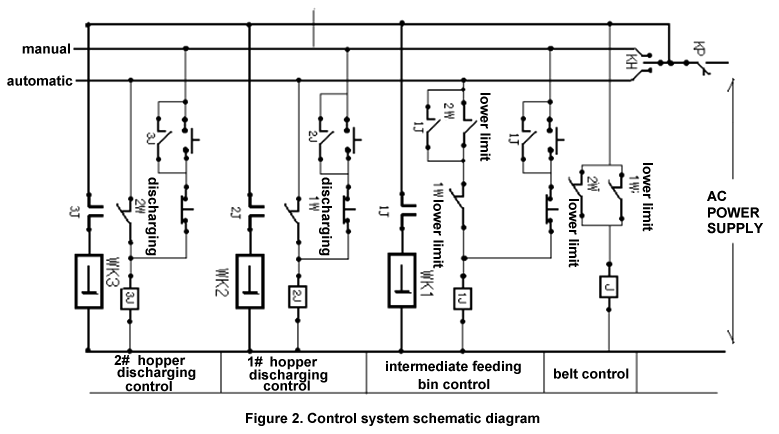
The flip plate inside the intermediate feeding bin and the material feeding and discharging valve of the two weighing hopper are single controlled, namely close when powered on and open when powered off, which is expressed with WK (WK1 refers to the flip plate inside the intermediate feeding bin, WK1 and WK2 refers to the material feeding and discharging valve of weighing hopper 1# and 2#), W refers to the contact output of the upper and lower control limits of the weighing controller. When the weighing weight reaches the set upper limit, the discharging contact (W discharge) opens to discharge material. It would not close till the lower limit. Feeding belt is controlled by contacts according to the requirements of electrical equipment, KH switch is used to select manual or automatic.
When the weighing hopper or other equipment (such as the flip plate, discharging valve) fails to work normally, the control signal in the weighing controller and control cabinet will be input to the control room to alarm and stop the tubing belt from working.
3. Video and remote devices
Two sets of video cameras are adopted. One is used to monitor the whole working state of weighing hopper. The other should be able to see clearly the cumulative weight displayed on two large screens.
Digital optical terminal is used for remote device. Special ASIC design and high-speed DSP technology are used in the Digital optical terminal, which provides an all digital compression-free and damage-free broadcasting transmission mode. High-definition and high-resolution are transmitted long-distance through optical fibers with high-quality and non-destructive. A pair of Digital optical terminal, connected with an optical core, is used to transmit the video signal, RS232 (or RS485) signal to metering room remotely.
II. Working Process
Lime powder conveyed by tubing belt fall into the 1# weighing hopper that is set with the lower limit (empty hopper) through the flip plate in the intermediate feeding bin. When the weight of lime powder in the weighing hopper reaches the upper limit setting (full bucket), weighing controller of the weighing hopper will output two signals. One signal controls the flip plate in the intermediate feeding bin, promoting it switching materials from 1# weighing hopper to the 2# weighing hopper. After the material stops feeding in 1# hopper, the weighing controller weighs. The current display weight automatically accumulates to the accumulative display. Another signal opens the discharging valve of 1# hopper to discharge materials. The 2# hopper is feeding at this time.
When the 2# hopper is feeding, the 1# hopper is discharging materials till its lower limit setting (empty hopper). At this time, the weighing controller of 1# hopper gives out the signal of empty hopper to close the discharging valve of 1# hopper. At this time, the 1# hopper is in waiting state.
When the 2# hopper is fed to the upper limit setting (full hopper), repeat the same operations as the 1# hopper.
Cumulative weight of the weighing controller is the automatic accumulation of each discharge value. The sum of cumulative weights of the two weighing controllers is the total weight of the material (lime powder) conveyed by tubing belt.
III. System Performance
The system adopts the closed double scale form, interlock control, low system integration cost, simple implementation and good environmental protecting performance. Since it puts into operation, it has performed well and achieved continuous, fast and accurate weighing. The commissioning of the system has accumulated a new method for tubing belt scale weighing.
I. Scheme and Composition
Basic design scheme: Material (lime powder) conveyed by the tubing belt is continuously conveyed to two weighing hoppers respectively, and the two weighing hoppers conducts static weighing in turn under a working mode of alternate loading and unloading, quick unloading and slow loading. The time interval from quick unloading and slow loading ensures the static weighing of weighing hopper while guaranteeing the continuous conveying of materials on the tubing belt, thus realizing the continuous, fast and accurate weighing measurement.
The system consists of two weighing hoppers, control devices, video and remote devices. The system structure of tubing belt scale is shown on figure 1.
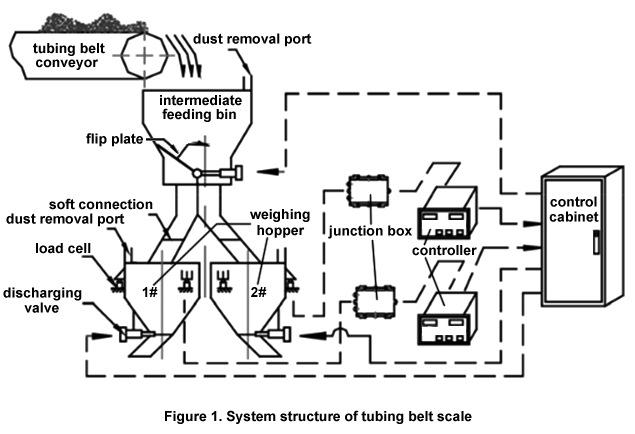
1. Weighing hopper
Weighing hopper is composed of load cell, weighing controller and limit device, configuration of the weighing hopper should meet the technical requirements of corresponding accuracy grade.
1.1 Selection of load cell
The load cell should be column type load cells or shear beam load cells with good side load and impact resistance, easy installation and maintenance.
The main technical parameters of column type load cells:
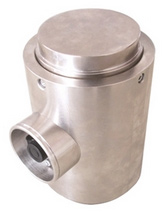
- Accuracy: 0.03%FS
- Sensitivity: 2.0mV/V
- Output impedance: 350Ω ± 3Ω
- Overload capacity: 150%
The main technical parameters:
- Linearity: 0.01%FS
- Input sensitivity: 0.2uv/d
- Full-scale input signal range: 0~10mV
- A/D conversion speed: 10 times/s
- Internal numbers of divisions: 1 million
- display number of divisions: 60000
- Zero temperature influence: ≤0.2μv/°C
- Full degree temperature influence: ≤10ppm/°C
-
Load cell excitation voltage: DC 15V ± 0.3V, maximum excitation current: 240mA.
- Automatic and manual calibration modes
- Two displays
- Batching control mode
- Keys for upper and lower setting
- Automatic digital accumulate function
- Relay control contact output (4 pairs of NO and NC)
- 4 standard analog output interface
- RS232 (or RS485) communication interface and 0-20mA output
-
Power failure protection.
The weighing system uses a collision-type limit device that is mounted near the load cell. The collision type limit can limit load cell movement on horizontal direction and provide support protection to the hopper on vertical direction due to the inclination of load cell. The load cell controller displays the accumulated weight on the large screen in the field through 0-20mA signal output. The system is well grounded to ensure that the system is effective in preventing lightning strikes.
2. Control device
The control device consists of intermediate feeding bin, material feeding and discharging valve and control equipment. A flip plate is set inside the intermediate feeding bin to control the material feeding of weighing hopper 1# and 2#, the material feeding and discharging valve may be electric or pneumatic.
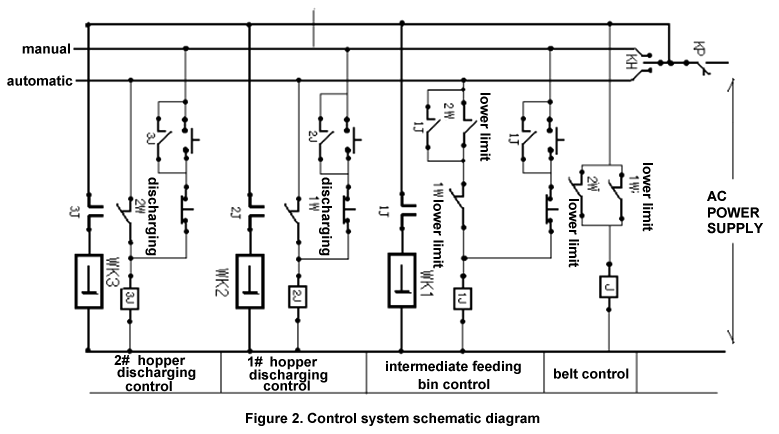
The flip plate inside the intermediate feeding bin and the material feeding and discharging valve of the two weighing hopper are single controlled, namely close when powered on and open when powered off, which is expressed with WK (WK1 refers to the flip plate inside the intermediate feeding bin, WK1 and WK2 refers to the material feeding and discharging valve of weighing hopper 1# and 2#), W refers to the contact output of the upper and lower control limits of the weighing controller. When the weighing weight reaches the set upper limit, the discharging contact (W discharge) opens to discharge material. It would not close till the lower limit. Feeding belt is controlled by contacts according to the requirements of electrical equipment, KH switch is used to select manual or automatic.
When the weighing hopper or other equipment (such as the flip plate, discharging valve) fails to work normally, the control signal in the weighing controller and control cabinet will be input to the control room to alarm and stop the tubing belt from working.
3. Video and remote devices
Two sets of video cameras are adopted. One is used to monitor the whole working state of weighing hopper. The other should be able to see clearly the cumulative weight displayed on two large screens.
Digital optical terminal is used for remote device. Special ASIC design and high-speed DSP technology are used in the Digital optical terminal, which provides an all digital compression-free and damage-free broadcasting transmission mode. High-definition and high-resolution are transmitted long-distance through optical fibers with high-quality and non-destructive. A pair of Digital optical terminal, connected with an optical core, is used to transmit the video signal, RS232 (or RS485) signal to metering room remotely.
II. Working Process
Lime powder conveyed by tubing belt fall into the 1# weighing hopper that is set with the lower limit (empty hopper) through the flip plate in the intermediate feeding bin. When the weight of lime powder in the weighing hopper reaches the upper limit setting (full bucket), weighing controller of the weighing hopper will output two signals. One signal controls the flip plate in the intermediate feeding bin, promoting it switching materials from 1# weighing hopper to the 2# weighing hopper. After the material stops feeding in 1# hopper, the weighing controller weighs. The current display weight automatically accumulates to the accumulative display. Another signal opens the discharging valve of 1# hopper to discharge materials. The 2# hopper is feeding at this time.
When the 2# hopper is feeding, the 1# hopper is discharging materials till its lower limit setting (empty hopper). At this time, the weighing controller of 1# hopper gives out the signal of empty hopper to close the discharging valve of 1# hopper. At this time, the 1# hopper is in waiting state.
When the 2# hopper is fed to the upper limit setting (full hopper), repeat the same operations as the 1# hopper.
Cumulative weight of the weighing controller is the automatic accumulation of each discharge value. The sum of cumulative weights of the two weighing controllers is the total weight of the material (lime powder) conveyed by tubing belt.
III. System Performance
- Opening of the weighing hopper's discharging outlet should be determined by the maximum flow rate of the tubing belt. It shall be guaranteed that the discharging flow is larger than the feeding flow, so as to realize the working mode of 'fast unloading and slow loading'.
- Alternating weighing and unloading of two weighing hoppers can not only greatly reduce the capacity of weighing hopper, but also reduce the required height difference. But the capacity of weighing hopper should be as large as possible according to the site conditions, thus the action frequency of flip plate in the intermediate feeding bin would greatly reduce, thus extending the service life of equipment.
-
The load cell should be installed on the load-bearing beam. When steel structure is used as load-bearing beam, it should have sufficient rigidity, otherwise reinforcement measures should be taken to strengthen the rigidity of beams.
In selecting the weighing hopper for three load cells, when the discharging outlet seriously deviates from the center of gravity of the hopper scale, load cells should be installed on both sides of the vertical bisector corresponding to the discharging outlet, so as to form an isosceles triangle. - Weighing hopper adopts a totally closed system, the feeding inlet, discharging outlet and dust removal device should be separated from each other with soft connection. When the material is a powder, discharging valve of the weighing hopper shall consider seal devices. Reduce dust and leakage to ensure accurate measurement.
- Cone part, shunt plate and flip plate in the weighing hopper, which are easy to be worn out by materials, shall add abrasion resistant layer on the surface, corresponding material for the abrasion resistant layer may be ultrahigh molecular weight polyethylene.
- Weighing hopper should set special rack for weight, so as to calibrate the weighing hopper regularly.
-
The system has two working modes: automatic and manual.
The system adopts the closed double scale form, interlock control, low system integration cost, simple implementation and good environmental protecting performance. Since it puts into operation, it has performed well and achieved continuous, fast and accurate weighing. The commissioning of the system has accumulated a new method for tubing belt scale weighing.