How to Choose Load Cell Connections?
The load cell is installed between the load receptor and the foundation installation surface. If the load cell is simply connected and thereafter used, it will not only not achieve the expected weighing accuracy, but also easily cause the damage of load cell and safety accidents. As a key component of weight measurement, load cell connections directly affect the accuracy of weighing measurement results. Moreover, the load cell connections also play a more important role in resisting all kinds of interference force in practical applications.
I. Interference force of weighing process
It's mainly reduced or eliminated by proper load cell connections.
The concentricity, size, surface roughness and material hardness of the connections structure will affect the accuracy of the load cell in use. The connections should have a high smoothness. Otherwise it will be deformed after being stressed. Table 1 lists the deformations of steel joints after grinding and planning. Table 2 shows the deformation of three different materials under 5 MPa pressure. The softer the connections material and the worse the smoothness, the greater deformation will occur under very small loads. Deformation of connections will change resultant force point and result in performance change of load cell.
Table 1. Deformations of steel joints after grinding and planning
Table 2. Deformation of three different materials under 5 MPa pressure
The selected load cell connections should have functions and manufacturing quality as follows:
Common load cell connection can be divided into the compression type and tension type.
1. Compression type connections
Compression type connections is special for compression load cells. They adopt a cylinder or spherical structure to transfer force value, that means the gravity generated by all heavy objects on the load receptor is transferred from the point contact of the sphere to the load cell, so that the gravity line coincide with the ideal stress axis of the load cell. Besides, the compression type load cell connection also has the following functions:
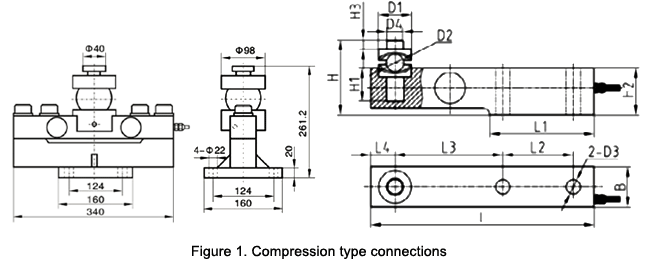
2. Tension type connections
Commonly used tension type connections are actually different kinds of universal coupling for tension load cells. They have excellent reset performance and always make the gravity line of the subject coincide with the ideal mechanical axis of the load cell, thus resisting lateral force interference in any direction. If a rotating device is equipped at the same time, any disturbance moment on the gravity line can be eliminated before the load is applied to the action point of the load cell. The tension load cell connection is connected by threads, for safety consideration, the thread size and length shall generally refer to Table 4 below. In figure 2, the tension type connections is for s type load cell (ATO-S-LCS-DYLY-102).
Table 4. Thread size and length reference table
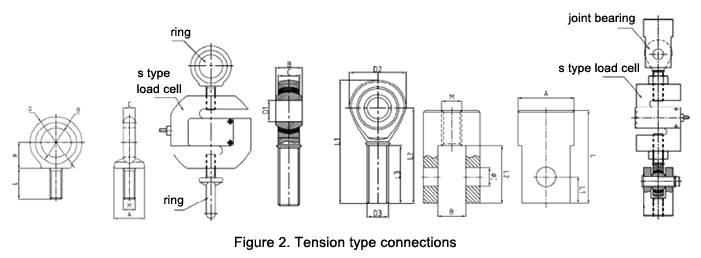
The stable and reliable operation of load cell can't be separated from the reasonable cooperation of load cell connections. According to the market feedback information collected over the years, most of the problems occurred in field application are caused by unreasonable selection and installation of load cell connections during installation. If the load cell is not equipped with a proper load cell connection, accuracy of the whole weighing system may be seriously low or unusable.
I. Interference force of weighing process
- When subjects are added onto the load receptor, load-bearing beam of the load receptor will inevitably produce disturbance to make the fulcrum produce a turning angle. If the load-bearing beam is not flexibly connected with the load cell, 'wrong signal' would occur inevitably, the load cell may also be damaged.
- When the weighed vehicle brakes as it enters the bearing platform, a considerable horizontal impact force will be produced. Although the stopper is installed, proper load cell connections are still necessary to ensure rapid reset, so as to reduce the impact force to the load cell as much as possible.
- Linear expansion coefficient of the load receptor and foundation installation surface are different in most cases, the transverse force produced by the change of ambient temperature will make the load cell to output unrelated weighing values.
- In installing large electronic scales, there must be a certain deviation in the installation position between the load receptor and the installation base surface, so the load cell connections should ensure a certain swing angle and displacement.
-
Load receptors are generally connected by welding. With time passes, irregular distortions will occur due to stress release, so the load cell connections shall also make proper changes in the shape and position.
It's mainly reduced or eliminated by proper load cell connections.
The concentricity, size, surface roughness and material hardness of the connections structure will affect the accuracy of the load cell in use. The connections should have a high smoothness. Otherwise it will be deformed after being stressed. Table 1 lists the deformations of steel joints after grinding and planning. Table 2 shows the deformation of three different materials under 5 MPa pressure. The softer the connections material and the worse the smoothness, the greater deformation will occur under very small loads. Deformation of connections will change resultant force point and result in performance change of load cell.
Table 1. Deformations of steel joints after grinding and planning
Surface processing type |
Flexibility m/N |
|
First load |
Second load |
|
Grinding |
0.00004 |
0.00002 |
Planing (feed amout s = 0.265) |
0.009 |
0.007 |
Planing (feed amout s = 0.55) |
0.29 |
0.00046 |
Planing (feed amout s = 0.8) |
0.006 |
0.00034 |
Materials |
Roughness (Ra) |
Surface deformation (μm) |
|
First load |
Second load |
||
Steel |
6.3 |
2.2 |
0.33 |
Copper |
6.3 |
3.6 |
0.38 |
Aluminum |
6.3 |
5.4 |
0.60 |
- Ensure the accuracy of weighing value to be transferred, ensure that the force of the load cell fits with its axis or is controlled within the allowable error range.
- In weighing operation, the load receptor produces horizontal displacement or impact, it will also generate irregular deformation due to stress release, expand at different temperatures due to the difference of linear expansion coefficient. At this time, the connections shall have flexible rotation and swing to ensure that the weighing values obtained by the load cell are real and effective.
- The load cell connections should also have certain stiffness in the direction of force. When a load is added, deformation of the connections shall be as smaller as possible.
- The connections should have a good automatic reset function.
-
The connections should have a certain roughness, so that it can ensure a contact stress smaller than the allowable contact stress under a large load while no depression occurs when it combines with a corresponding hardness. The friction force and friction moment produced will not affect its flexibility.
Common load cell connection can be divided into the compression type and tension type.
1. Compression type connections
Compression type connections is special for compression load cells. They adopt a cylinder or spherical structure to transfer force value, that means the gravity generated by all heavy objects on the load receptor is transferred from the point contact of the sphere to the load cell, so that the gravity line coincide with the ideal stress axis of the load cell. Besides, the compression type load cell connection also has the following functions:
- Good automatic reset function. In the weighing system, the load cell will always have a slight lateral impact and movement (the serious impact caused by excessive impact force needs to be overcome by special stoppers) when the load receptor bears a heavy object, which makes the action point of gravity on the load cell to deviate from the axis and thus cause the weighing errors.
-
Safety protection and fatigue resistance function. The load cell connection is installed between the load receptor and the load cell in a movable connection state. If there is no restraint device, the load receptor will get rid of the load cell and damage the weighing system under strong external impact. Generally, steel ball and concave sphere as shown in the figure are used for loading. Design and selection principles had better to refer to table 3. In figure 1, the left is compression type connection for 50 ton shear beam load cell (ATO-S-LCB-TJH-6A). The right is for cantilever beam load cell.
Rated load |
500kg~2 ton |
5~10 ton |
20~50 ton |
Diameter of steel ball (mm) |
25.4 |
38.1 |
76.2 |
Radius of concave spherical (mm) |
32 |
45 |
65 |
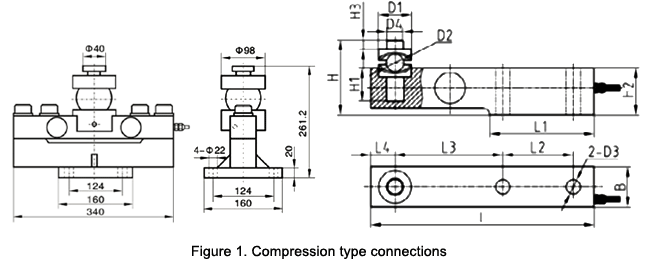
2. Tension type connections
Commonly used tension type connections are actually different kinds of universal coupling for tension load cells. They have excellent reset performance and always make the gravity line of the subject coincide with the ideal mechanical axis of the load cell, thus resisting lateral force interference in any direction. If a rotating device is equipped at the same time, any disturbance moment on the gravity line can be eliminated before the load is applied to the action point of the load cell. The tension load cell connection is connected by threads, for safety consideration, the thread size and length shall generally refer to Table 4 below. In figure 2, the tension type connections is for s type load cell (ATO-S-LCS-DYLY-102).
Table 4. Thread size and length reference table
Rated load |
20~100kg |
200kg~1 ton |
2~5 ton |
10 ton |
20 ton |
50 ton |
100 ton |
200 ton |
300 ton |
500 ton |
Connection thread (mm) |
M10*1.25 |
M12*1.75 |
M24*2 |
M39*2 |
M52*2 |
M76*3 |
M100*3 |
M150*4 |
M190*4 |
M240*6 |
Thread length (mm) |
15 |
15 |
30 |
50 |
65 |
115 |
150 |
200 |
250 |
300 |
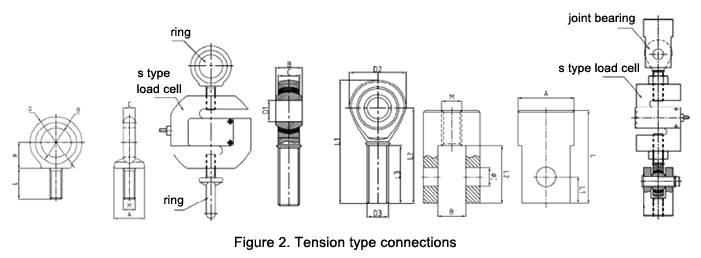
The stable and reliable operation of load cell can't be separated from the reasonable cooperation of load cell connections. According to the market feedback information collected over the years, most of the problems occurred in field application are caused by unreasonable selection and installation of load cell connections during installation. If the load cell is not equipped with a proper load cell connection, accuracy of the whole weighing system may be seriously low or unusable.